The presence of a shipwreck in deep waters off the Dry Tortugas first gained attention in 1965 when the shrimp trawler Trade Winds snagged various colonial-era Spanish artifacts in its nets. At the time the depth of the water (405 meters) made exploration of the site impractical.
By the late 1980s underwater technology was developing at a rapid rate when Seakhawk Deep Ocean Technology discovered the site, which was nicknamed “Tortugas” using a Deep Ocean Engineering Phantom ROV. Historically, the "Tortugas" excavation was the world's first deep-ocean remotely-operated archaeological excavation of a shipwreck site. Nearly 17,000 artifacts, including some as small as seeds and pearls, were recovered from the site during the 1990-1991 excavation seasons.
To conduct a survey of the site, the company engaged the 26-meter RV Seahawk, equipped with side-scan sonar, sector-scanning sonar, magnetometer, a multi-target acquisition/tracking system, an integrated navigation system, Remotely-Operated Vehicles, HF, VHF radios and a very long range cellular telephone. The integrated navigation system was capable of generating search grids and graphically displaying the real-time position of the research ship.
The side-scan sonar featured transducers on a tow fish that emitted and received acoustic pulses, which were transmitted to the research vessel. The data from the side-scan sonar tow fish were transmitted to a recorder for processing. The system was able to record a swathe of up to 300 meters to each side, depending on the frequency. Conditioned by density and material, features and objects rendered a dark silhouette created by acoustic shadows on thermal paper, which fed out of the recorder at a speed proportional to the tow fish’s movements along the survey lines. The resulting image provided a detailed representation of the ocean floor features and characteristics: an accurate picture of a wide area, which could be interpreted to construct a three dimensional image of the seafloor’s contours.
Aboard the Seahawk were three ROVs equipped with video and still cameras to provide visual access and documentation in deep water, and a manipulator device that enabled the mechanical retrieval of artifacts. The largest and most versatile of the ROVs was the custom-built Phantom DHD2 which had a depth rating of 610 meters, a low-light color video camera and relatively simple articulated arm. A Phantom 500, with a depth rating of 150 meters and a color video camera, was a mid-range ROV. Finally, a Phantom 300, with a depth rating of 90 meters and color video, functioned in shallow water. The Seahawk was capable of holding station under its own power without anchoring by ‘liveboating’ the vessel during ROV operations.
Initial visual survey of the wreck site was accomplished using the Phantom DHD2 ROV, which was equipped with a Mesotech 971 sector scanning sonar and was utilized to define the location and perimeter of the site. The ROV was linked to Seahawk via 610 meters of shielded 42 separate conductor umbilical cable (no single wire multiplex control system was available in 1990-91) and was fitted with two 250-watt halogen lights and two Panasonic CCD low light video color cameras to illuminate the site.
The Phantom DHD2 had a single function manipulator arm to provide dexterity for the retrieval of artifacts and was equipped with an ORE multi-beacon, which emitted an analog signal received by a Trac Point II tracking system. The pilots flew the ROV using a ‘joy stick’ control and observation via a small TV monitor mounted in the control console. A ‘co-pilot’ managed the camera adjustments, recorders and manipulated the retrieval arm.
The launch system onboard the RV Seahawk consisted of a winch, an A frame, armored tether and depressor weight that allowed ROV operations to be conducted in depths of up to 600 meters of water. The ROV was free-swimming, relying on the depressor weight connected to the armored umbilical, with a 50 meters neutrally buoyant excursion tether from the depressor that provided a 100 meters footprint for the ROV.
The video survey of the “Tortugas” deep-water wreck initially revealed a shipwreck site measuring approximately 15m long and 10m wide characterized by wooden hull remains, piles of ballast stone and numerous 17th-century olive jars.
In order to commence excavations with suitable technology, a second vessel, the 64m-long Seahawk Retriever, was dispatched to the site in May 1990. After lengthy consultation with archaeologists and subsea engineers, a large work ROV, nicknamed Merlin, was designed and constructed to the specifications laid out by Seahawk’s technology team specifically for archaeological excavation in deep water.
Merlin was fitted with advanced Schilling manipulators, a customized suction dredge, an acoustic long baseline positioning system and weighed approximately three tons out of water. Buoyancy blocks of syntactic foam (to resists the crushing effects of pressure at 400m) made Merlin 272kg positively buoyant. The ROV had six hydraulic powered positioning thrusters; vertically oriented thrusters allowed it to work above the seafloor without stirring up sand or silt.
The thrusters also held the ROV steady when artifacts were lifted. Either manipulator arm could lift up to 113kg without affecting Merlin’s position in the water. One of the manipulators used a system controlled by a master replica of the manipulator at the surface desk; the jaw pressure could be dialed up to 500lbs or reduced to a few ounces. Positioning was determined and recorded by a system of long baseline transponders installed on the site, which communicated with transponders on Merlin and the ship.
A crew of three technicians operated the ROV from the control room on board the Seahawk Retriever under the supervision of the project archaeologist. Video was relayed to the control room via fiber optic cable, where three 30in video screens provided a 180-degree view of the underwater excavation site. Pilots watched events on the seafloor live in real time on monitors and commanded the manipulator arms using joysticks at the control console aboard the Retriever.
Two Schilling Titan manipulators were fitted to ROV Merlin. One was a seven-function position feedback unit used for all delicate operations. The other was a Schilling Titan five-function unit utilized mainly for holding the sediment removal nozzles and for lifting artifacts already contained in baskets. The seven-function unit was controllable by the operator in jaw grip pressure ranging from a few ounces to 45kg. The main arm could lift object weighing up to 226kg. Perhaps the most resourceful modification custom made for the project was the attachment to the ROV of a small, 5cm-diameter bellows type suction cup. The suction delivered to this device was controllable by the operator. The cup could pick up the most delicate porcelain and olive jars without causing damage, yet could still remove large angular ballast stones. The invention and adoption of this limpet system on the Tortugas shipwreck went through several phases of on-site development and was the first application of this tool on a deep-sea archaeological excavation.
Artifacts were initially secured in circular fishing baskets, which were numbered for input into the database and for recording onto videotape. They were fitted with ‘jug’ handles on the sides and ‘bucket’ handles on top to facilitate carrying by the ROV manipulator arms. The baskets were placed in sectioned off partitions in the large steel basket designed for retrieving artifacts from the sea bottom, nicknamed the 4Plex, which had a lifting capability of three tons. When the 4Plex was ready for recovery, a wire was lowered from the research vessel’s recovery winch. Near the hook on this wire was a transponder that enabled the ship to reposition itself using its winches to guide the hook to within 50m of the 4Plex. When the hook arrived near the sea bottom the ROV approached it, grasped it with a manipulator and conveyed it to the 4Plex, where it could be hooked on and lifted to the ship.
After recovery, an empty 4Plex would be sent down again with a transponder on the wire. The transponder relayed depth, thus permitting its descent to be halted just above the seabed. The ROV then pushed the 4Plex to the appropriate position before it was lowered completely onto the seabed. Merlin finally unhooked the wire from the 4Plex to allow the empty wire to be winched back to the surface. Due to the careful navigation of the ROV using the positioning system, at no time during the excavation were any entanglement problems encountered between the ROV umbilical and the 4Plex lift wire during deployment or recovery operations.
The sediment removal and filtration (SeRF) system used on the Tortugas excavation was a 25hp hydraulically driven three-stage water pump. This venture pulled water and unobserved small finds through the main system. No artifacts passed through any mechanical portion of the pump, so there was no damage to cultural remains that might have traversed the system. In addition to working sensitively around archaeological remains, this system could extract solid clay at full power. It could also be reversed to back flush the system or blow away silt and sand.
During the excavation of the site the project archaeologist directed all activities undertaken by the ROV technicians. One of the key benefits of this remote system, as opposed to archaeological excavations by divers, was the ability of the entire team to view, discuss and contemplate the excavation strategy. This unique ability to share ideas during the course of the excavation was exceptionally useful when nearly every activity on the site required the development of new techniques and tools. The fact that every second of the excavation was recorded on video allowed thorough review and documentation of the project two decades after the excavation took place.
After ten months of excavation, thorough documentation of the site and recovery of just under 17,000 artifacts, the Seahawk team proved that it was possible to undertake a detailed archaeological excavation remotely using robotics, something never before accomplished. More than just allowing a primitive excavation, as one would expect from the inaugural attempt at such a complex task, the systems designed and utilized on this project provided a level of repeatable accuracy, artifact recovery and efficiency of recording that would serve to provide a model for the evolution of robotic excavation in the deep ocean for future generations.
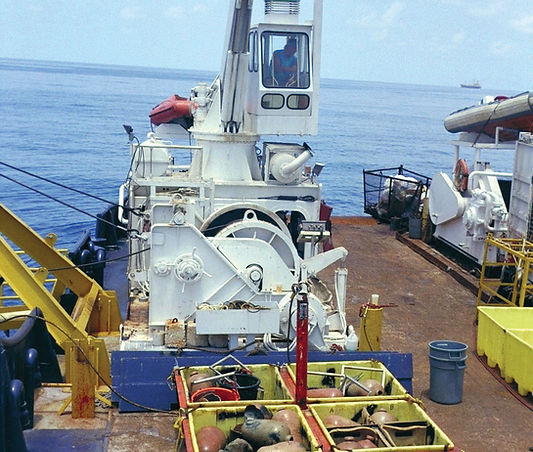
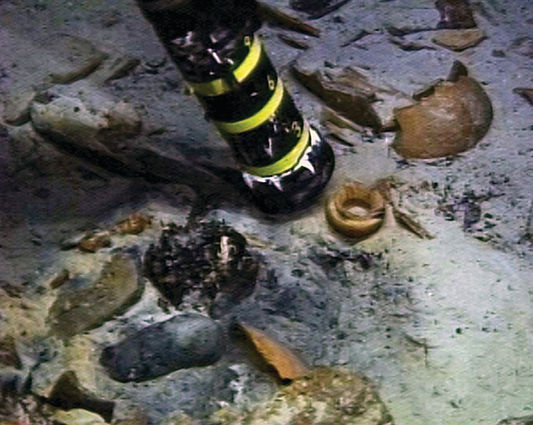

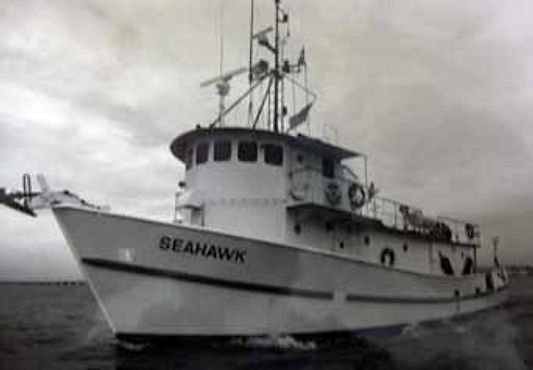



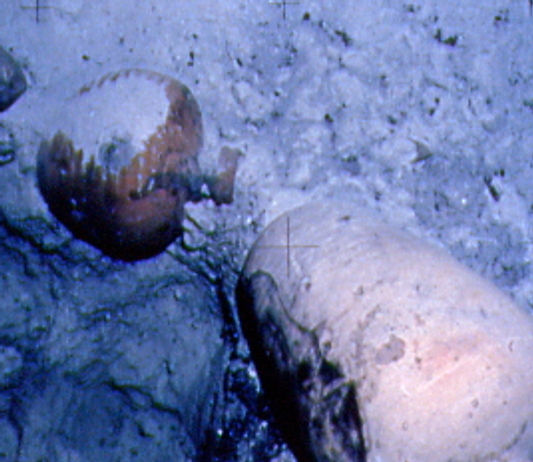
